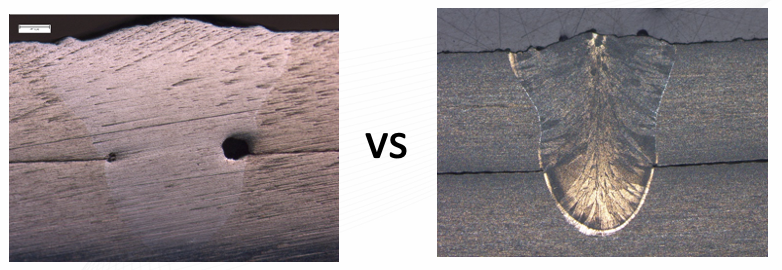
Last month, Civan Lasers CEO, Eyal Shekel, presented a proof of concept to the attendees at the EALA – European Automotive Laser Applications - Conference in an online session together with Valeo’s Jesús Jiménez Palacios, their Senior R&D Expert for Welding/Laser.
Valeo is seeking joining technology for the next generation of larger battery coolers for EVs. Currently, Valeo is using a brazing process for welding battery coolers, but are looking for a solution that can provide high quality results at 15m/min for large parts. The existing beam shaping and wobble solution were tested and could not effectively produce a quality weld at this speed.
Together with AIMEN, Civan and Valeo set up a testing process in Civan’s applications lab to create a leakproof weld for the Al 3003 battery coolers.
Using Dynamic Beam Lasers, each of the variables were isolated and then tested to find the optimal:
Power for penetration depth
Beam Shape for satisfactory seam width at a speed of 15m/min
Shape frequency to eliminate spatter
Once the variables were determined, samples were welded and tested for leaks in liquid. The optimal results were achieved with an hourglass beam shape with a frequency of 225kHz. The sample passed the leak test.
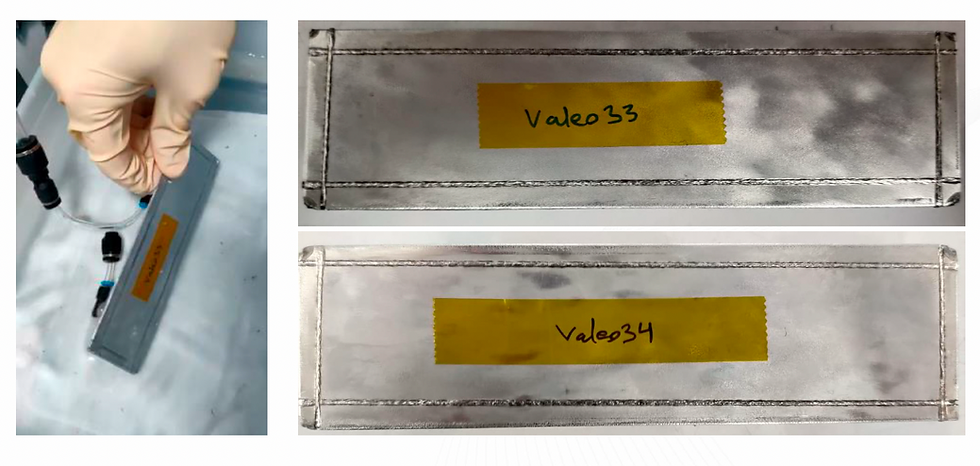
CONCLUSIONS This test proves that Dynamic Beam Lasers can be a viable solution for the Al 3003 battery coolers. Effective welding of the materials at a rate of 15m/min was achieved with no spatter. The isolated control of beam shapes and frequency allowed for very fast process development. It also showed how spatter can be significantly reduced when adjusting the beam shape and frequency. Testing will find the optimal combination to achieve high quality results even with crack sensitive materials. Want to hear more? Contact us at https://www.civanlasers.com/contact-us