Solving Cracking, Porosity and More in Laser Welding
- Ami Spira
- Jul 6, 2021
- 5 min read
This blog was written in conjunction with Florian Hugger from BBW Lasertechnik, the leading innovative laser material processing experts
Automotive manufacturers use laser welding on a daily basis to create integral vehicle parts that must pass rigorous safety standards.
Laser welding has proven to be very powerful in steelwork. However, as the automotive industry shifts to e-mobility, automotive parts use much more copper and aluminum for the required electronic components. The increased thermal conductivity and low absorption of those materials leads to distortions and defects in the final weld.
Here are 5 main challenges in the automotive parts laser welding:
Cracking in Metals
Especially when welding aluminium alloys and high-carbon steels, cracking is a common defect that renders parts unusable.
Hot and cold cracks are formed when the laser makes the parts pull apart by thermal shrinkage, so what’s needed is a laser on either side of the weld in order to push the parts back together to counteract the shrinkage that would cause cracking.
The current solution is to induce a second heat field, by using either an additional laser or via induction heating.

(source Göbel, G: Erweiterung der Prozessgrenzen beim Laserstrahlschweißen heißrissgefährdeter Werkstoffe)
A second laser is preferable because minimal heat is being used very locally, but a second laser is very expensive. Induction heating is more economical, but you must heat the entire part which means there is a huge amount of heat going into the material leading to high distortion.

(source Göbel, G: Erweiterung der Prozessgrenzen beim Laserstrahlschweißen heißrissgefährdeter Werkstoffe)
A lesser used solution are DOEs (diffractive optical elements). DOEs are inflexible and only offer one shape and movement in a single direction.
To truly solve the challenge of cracking, we need a flexible laser that can provide a primary heat spot for the weld with two secondary heat spots keeping the metal pushed together.
Porosity
Porosity is caused by an unstable keyhole and the collapse of the vapor capillary. Different techniques are being tried in order to create a more stable keyhole and reduce porosity, but an ideal solution has yet to be found.
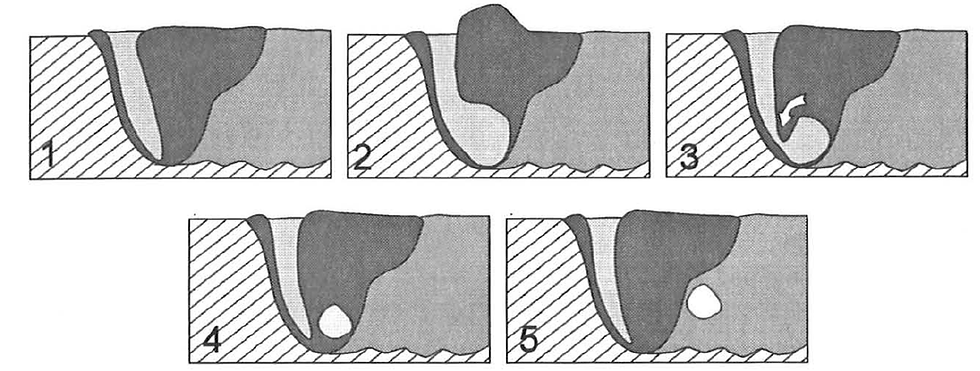
(source Hohenberger B.: Laserstrahlschweißen mit Nd:YAG-Doppelfokustechnik)
Oscillation with a scanner at a very high speed can work to stabilize the keyhole, but the shapes that can be used are inflexible. The most common shape for oscillation is a spiral, but it is not fast enough to prevent porosity and its inflexibility limits its potential.

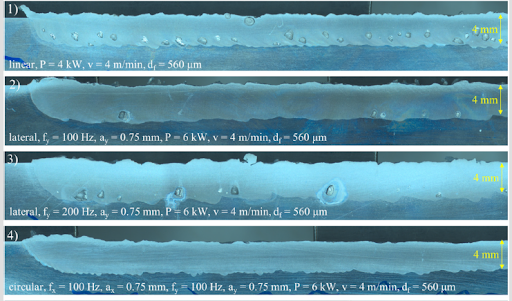
(source Fetzer et al.: Reduction of pores by means of laser beam oscillation during remote welding of AlMgSi)
Another option to stabilize the keyhole is to try to open the keyhole at the top to improve degassing. This means changing the keyhole from an “I” shape to a “V” shape, which is currently done using multicore fibers. Similar to oscillation, this solution is inflexible because it can change the power of the inner and outer fiber cores, but cannot change the size or shape of the keyhole.

(source Leimser, M: Strömungsinduzierte Einflüsse auf die Nahteigenschaften beim Laserstrahlschweißen von Aluminiumwerkstoffen)
Finally, power modulation has also been tried as a way of stabilizing the keyhole. This solution is limited because it does not allow for varying levels of evaporation on either ends of the keyhole.
Right now, we do not know what could be the best solution to prevent porosity because testing is limited by the inflexibility of the lasers. Once we can overcome this barrier and test various beam shapes and rotating heat spots, we will be able to test for an optimal solution.
High-Speed Welding
A higher speed of welding means a higher likelihood of defects. Usually, the weld is limited to a speed of ½ m/sec while anything above that causes humping and undercuts because the velocity of the melt is too high.
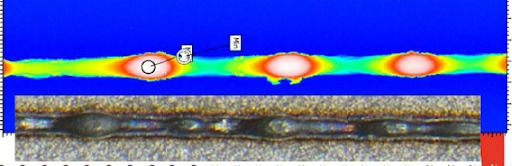
700 mm/s Single-spot (from BBW)
The situation is slightly improved with double-fiber lasers because the additional heat source creates a larger melt pool which is slower and more stable.
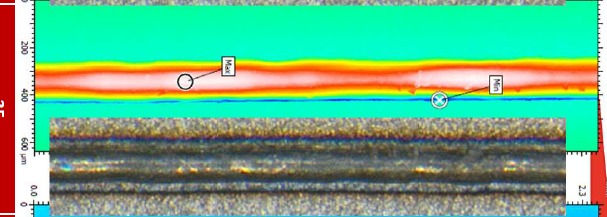
700 mm/s Multi spot (source BBW)
Beam oscillation with a scanner is not possible at such high speeds as in the low frequency the spiral stretches out and cannot serve its purpose.
Here again, the inflexibility of today’s technology prevents the testing of new beam shapes and frequencies to find the optimal solution.
Dissimilar Metals
When welding metals of different types - i.e. aluminum and copper or copper and steel - the objective is a homogenous weld, but often the scanner is too slow to make this happen. When materials are intermixed improperly, the result is brittle faces and cracking, particularly when dealing with aluminum and copper.

(source BBW)
It is possible to weld dissimilar metals when both are very thin (0.5 mm). In this case, less power is needed and a scanner with smaller mirrors can go fast enough to create a solid weld. But, as soon as we are dealing with metals that are even 1 mm thick, a larger scanner would be needed which cannot move fast enough.
Dynamic Beam Shaping would allow the use of 2 laser spots to move at the same time (similar to the movement of a kitchen mixer) and provide the homogenous weld that is needed.
Asymmetric Parts
When welding two pieces of different thicknesses (such as one machined part that is thick and one thin sheet metal), an asymmetric heat field is needed. Because such a thing does not exist, the solution is to use the amount of heat required for the thick part despite the fact that it is too much for the thin piece.
The problem with this is that the more heat that is used, the more distortion there will be. This is a main reason why lasers are used for welding, in order to reduce the heat input. But, when there are asymmetric parts there is currently no solution that generates the right amount of heat for each part.
A second challenge related to asymmetric parts is that of gap-bridging - when there is a gap between two parts that needs to be sealed. If, for example, the gap is 50 microns and the laser beam is also 50 microns, it will go straight through the middle and will not seal the edges. The way to solve this situation is either to use a larger laser spot or beam oscillation.

(source Hohenberger B.: Laserstrahlschweißen mit Nd:YAG-Doppelfokustechnik)
The problem arises when the parts differ and the gap sizes may be smaller or larger - current laser heads are not flexible to adjust for varying gap sizes.
Laser Welding with Dynamic Beam Lasers
Right now, laser welding is limited by rigid technology. Flexible beam shapes will allow for full testing of many creative solutions that today cannot even be attempted.
Dynamic Beam Lasers provide the flexibility needed to solve these challenges:
Beam Shaping – Using simple software, quickly and easily design any beam shape.
Shape Frequency – Control the frequency of the beam shape from 400Hz –50MHz, which opens a new set of parameters to control the keyhole and melt pool.
Shape Sequence– Design a sequence of shapes to maintain the desired shape orientation relative to the feed direction.
Focus Steering– In addition to the inherent large depth of focus of the SM beam, shift the focus up to 50MHz without any mechanical components.
Dynamic Beam Lasers are the next generation of lasers that will help manufacturers rise above these key welding challenges and produce high quality parts.